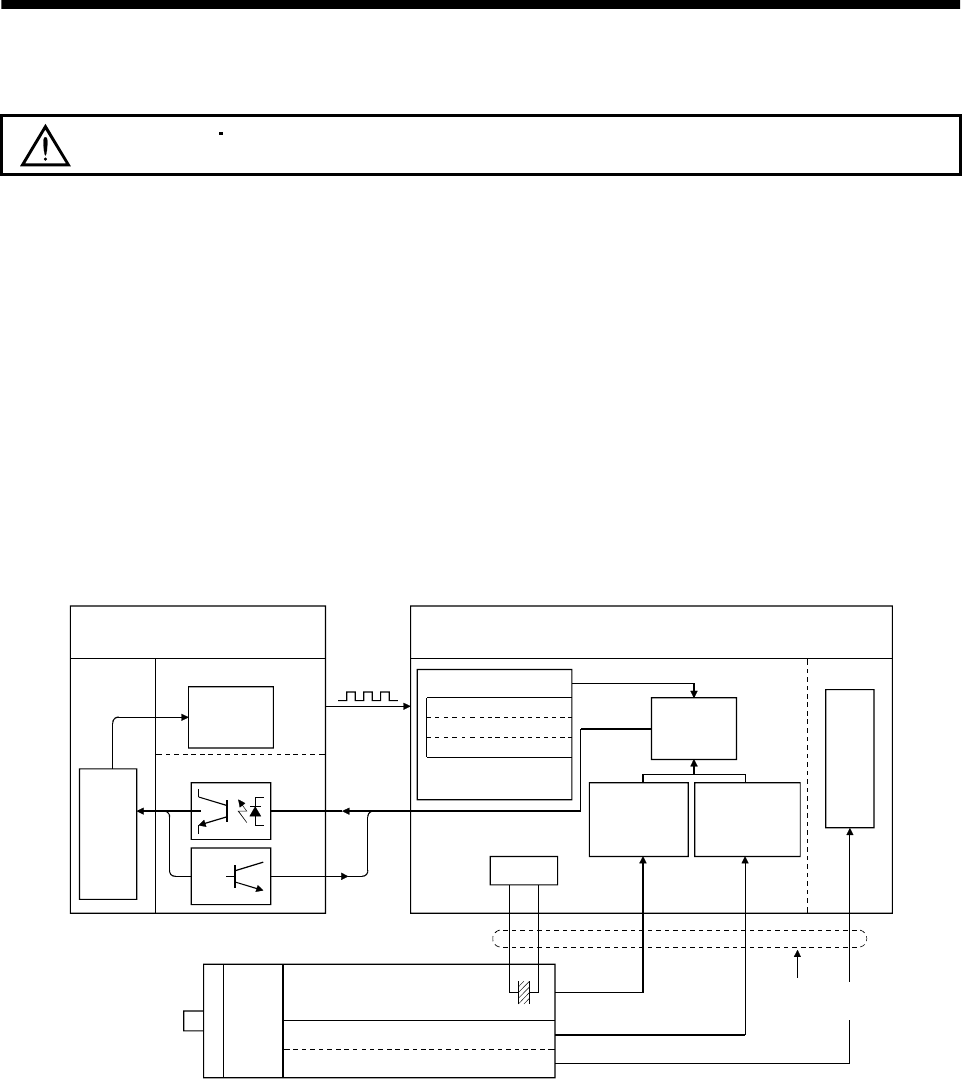
15 - 1
15. ABSOLUTE POSITION DETECTION SYSTEM
15. ABSOLUTE POSITION DETECTION SYSTEM
CAUTION
If an absolute position erase alarm (AL.25) has occurred, always perform home
position setting again. Not doing so can cause runaway.
15.1 Outline
15.1.1 Features
For normal operation, as shown below, the encoder consists of a detector designed to detect a position
within one revolution and a cumulative revolution counter designed to detect the number of revolutions.
The absolute position detection system always detects the absolute position of the machine and keeps it
battery-backed, independently of whether the general-purpose programming controller power is on or off.
Therefore, once the home position is defined at the time of machine installation, home position return is
not needed when power is switched on thereafter.
If a power failure or a fault occurs, restoration is easy.
Also, the absolute position data, which is battery-backed by the super capacitor in the encoder, can be
retained within the specified period (cumulative revolution counter value retaining time) if the cable is
unplugged or broken.
LSO
1XO
MR-BAT
CPU
General purpose programmable
controller
Servo amplifier
Pulse train
(command)
Changing the
current position
data
Positioning module
I/O module
Current
position
data
Input
Output
Home position data
EEPROM memory
Backed up in the
case of power failure
Current
position
data
Detecting the
number of
revolutions
LS 1X
Detecting the
position within
one revolution
Position control
Speed control
Servo motor
1 pulse/rev Accumulative
revolution counter
Super capacitor
Within-one-revolution counter
A, B, Z phase signals
(
Position detector
)
High speed serial
communication
Battery
15.1.2 Restrictions
The absolute position detection system cannot be configured under the following conditions. Test
operation cannot be performed in the absolute position detection system, either. To perform test
operation, choose incremental in parameter No.1.
(1) Speed control mode, torque control mode.
(2) Control switch-over mode (position/speed, speed/torque, torque/speed).
(3) Stroke-less coordinate system, e.g. rotary shaft, infinitely long positioning.
(4) Changing of electronic gear after home position setting.
(5) Use of alarm code output.